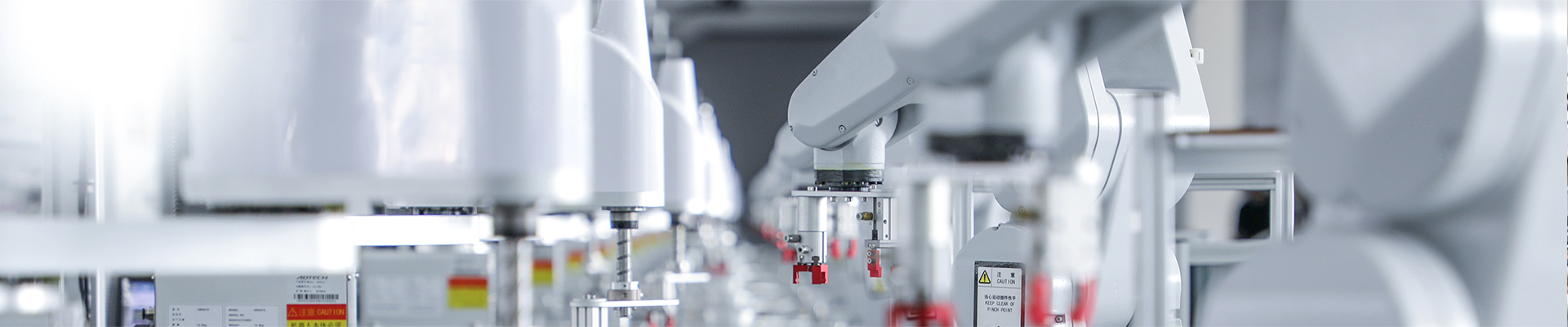
What role do cable lubricants play in underground cable pulling, and how do you select the correct type for different cable and conduit materials?
2025-07-19Cable lubricants are absolutely essential for efficient and safe underground cable pulling. They play a critical role in reducing friction, lowering pulling tensions, and ultimately protecting the cable and conduit from damage.
I. The Role of Cable Lubricants:
-
1. Friction Reduction: The primary function is to create a slippery film between the cable jacket and the inner wall of the conduit. This significantly reduces the coefficient of friction (COF), which is the force resisting movement.
-
2. Lowering Pulling Tension: By reducing friction, lubricants drastically lower the required pulling force. This helps stay within the cable's Maximum Allowable Pulling Tension (MAPT), preventing stretching, scuffing, or internal damage to conductors and insulation. It also reduces stress on pulling equipment.
-
3. Preventing Cable Damage: Reduced friction minimizes abrasion, nicks, and scrapes on the cable jacket, which could compromise its protective layers and lead to premature failure. It also lowers sidewall pressure (the force exerted by the cable on the conduit wall at bends), reducing the risk of damage at these critical points.
-
4. Easier Installation: Facilitates smoother, faster pulls, especially for long runs, multiple cables in one conduit, or conduits with many bends.
-
5. Future Removal/Replacement: A well-lubricated cable is often easier to remove from the conduit decades later, simplifying future maintenance or upgrades.
II. Selecting the Correct Lubricant Type:
The selection of the correct lubricant is critical for compatibility and performance. Using the wrong lubricant can cause severe damage to the cable jacket and insulation. Key considerations include:
-
1. Cable Jacket Material: This is the most important factor. Common jacket materials include:
-
PVC (Polyvinyl Chloride): Generally compatible with most water-based or polymer-based lubricants.
-
PE (Polyethylene) / HDPE (High-Density Polyethylene): Good compatibility with most standard lubricants.
-
XLPE (Cross-Linked Polyethylene): Requires lubricants specifically tested for XLPE compatibility.
-
LSZH (Low Smoke Zero Halogen): These environmentally friendly jackets require specially formulated lubricants that won't compromise their fire-retardant properties or emit harmful substances.
-
Rubber/Neoprene: May react adversely with certain oil-based lubricants.
-
Fiber Optic Cables: Often have delicate jackets and require highly compatible, non-gelling, and easy-to-clean lubricants.
-
-
2. Conduit Material: Common conduit materials include:
-
PVC: Most lubricants are compatible.
-
HDPE: Most lubricants are compatible.
-
Steel/Aluminum: Compatibility is less of an issue, but the lubricant must be effective on metal surfaces.
-
Fiberglass: Requires lubricants that won't degrade the resin.
-
-
3. Lubricant Composition:
-
Water-Based (Polymer-Based): The most common and versatile type. They dry to a thin, non-conductive film and are generally compatible with a wide range of cable and conduit materials. They are easy to clean up. Our recommended lubricants are typically high-performance, water-based formulas.
-
Wax-Based / Oil-Based: Less common for general cable pulling due to potential incompatibility with certain jacket materials, tendency to leave sticky residues, and difficulty in cleaning. Should generally be avoided unless explicitly approved by the cable manufacturer.
-
Specialty Lubricants: For very specific applications (e.g., fiber blowing, high-temperature environments), specialized lubricants may be required.
-
-
4. Temperature Range: Some lubricants perform better in specific temperature ranges. Extremely hot or cold conditions can affect their viscosity and effectiveness.
-
5. Manufacturer Recommendations: Always consult both the cable manufacturer's recommendations and the lubricant manufacturer's compatibility data (e.g., IEEE 1210 testing) before selection.
III. Application Techniques:
Proper application is as important as selection. Lubricant should be applied continuously at the feeder end, and often at intermediate points (e.g., manholes, long pulls), to ensure a consistent film throughout the entire conduit length. Over-lubricating is rarely an issue; under-lubricating is a common cause of pulling problems.
Our comprehensive supply chain includes a range of high-performance, tested, and compatible cable lubricants designed to work seamlessly with our cable pulling equipment and various cable types, ensuring optimal installation performance and long-term cable integrity.